Tack Coat
The absence or poor bonding between asphalt layers will reduce the service life of the pavement. Roffe and chaigon suggested that no bonding between the asphalt layer will reduce the service life of the pavement by 60%.
The most common tack coat materials are slow-setting asphalt emulsions (ss-1, ss-1h, CSS-1, and Css-1h). The using of rapid setting asphalt emulsions such as Rs-1, Rs-2, CRS-1, and CRS-2 are increasing in recent years. Asphalt emulsions producing a strong bond compared to cutbacks materials. Disadvantages of asphalt emulsions are the time required for setting and break of material. Also, material tracking and transference to the adjacent pavement. Tack coat break is the moment when enough water separates from the tack coat to show color change to black or brown. The break and setting time of asphalt emulsions affected by climate, rate of application, and the dilution of asphalt emulsion. The high rate of application of the tack coat will increase the break and setting time of asphalt emulsion. Certainly, diluted asphalt emulsion will require a longer time to set and break because the amount of water is more.
Tack coat application rate will vary according to surface condition. The rate of application will increase by the increase of surface roughness and weathering. Asphalt institute suggests the following table showing the application rates for different surface types.
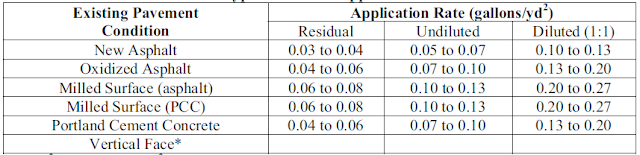
Table 1
Surface shall be prepared before applying a tack coat. The surface should be clean and dry to ensure maximum bonding. For old pavement, milling is recommended. The milling process will remove the upper layer of asphalt. Clearly, this layer is weak because it is subjected to heavy traffic and weathering conditions. Also, the milling will produce a smooth surface by removing all irregulates in the existing pavement. Milling will increase the surface area for tack coat by increasing surface roughness. Surface roughness will contribute to improving bonding between asphalt layers. The surface preparation for new pavement is minimal. Sweeping is sufficient before applying a tack coat. However, if the asphalt layer gets dirty, proper cleaning shall be done before proceeding with the next activity. Tack coat will be applied following appropriate surface preparation. Tack coat should be applied uniformly, and it should cover the surface in transverse and longitudinal directions. In the past, tacks coats were diluted to help in achieving uniform coverage of surfaces. The development of distributors' trucks eliminates the need for diluting tack coats. It is not recommended to dilute tack coats at the field because we need to know the amount of water precisely to calculate the residual tack coats.
The tack coat shall be distributed properly and uniformly. To prevent streaking and ensure proper application and coverage of prime coat. The spray nozzles shall be set at 15-30 from the horizontal axis of the spray bar, as shown in figure no: 1. Proper setting of spray nozzles will prevent the tack coat from interfering with the adjacent spray nozzles. The height of the spray bar should be adjusted to ensure at least a single, double, or triple overlap. For uniform applying of prime coat, the spray bar height must be maintained. Figure no:2 shows the effects of spray bar height on tack coat coverage.
Figure 1
Figure 2
Comments
Post a Comment